CASE STUDY 1
Cooling tower blow down treatment
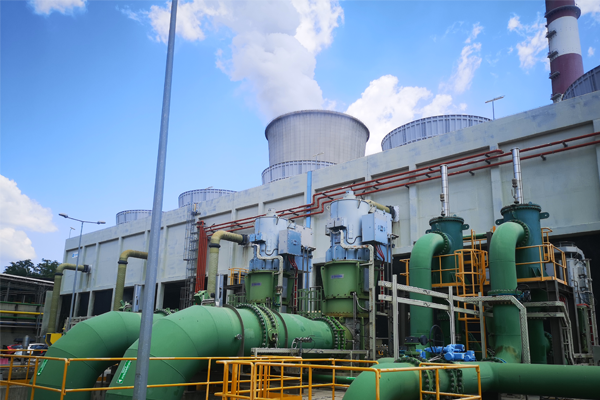
Water abstractions for the manufacturing industry and for production of electricity (primarily cooling water) account for more than 50 % of total gross abstractions in most EU countries. Europe still meets around 60 % of total electricity demand from thermal power (Eurostat, online code: nrg_105a). Every year, roughly 90.000 million m3.13of freshwater is abstracted to generate this energy. Cooling towers are an important component of refrigeration systems. They are common in industries such as oil & gas, chemical processing, power plants, etc. In a typical cooling tower, water is pumped from the tower basin (cooling water) and routed through the process. The warm water returns to the top of the cooling tower and trickles downward over the fill material inside the tower. As it trickles down, it contacts ambient air rising up through the tower by forced draft. That contact causes a small amount of the water to be lost as windage or drift and some the water evaporates.
During evaporation, the contained salts are left behind raising their concentration in the circulating cooling stream. If this process is continued (cycle of concentration), less soluble minerals such as calcium, magnesium and silica may precipitate as insoluble salts causing scaling. To prevent undesired rise of salt(s) concentration, a portion of the water is drawn off or blown down for disposal. Fresh water make-up is supplied to the tower basin to compensate for the loss of evaporated water, the windage loss water and the blow down water. The PPC’s cooling tower is of wet induced draft counter flow type. The tower requires a considerable amount of water as their make-up supply (750 m3/h.) which accounts for >95% of the plant’s total water abstractions. Also, the cooling tower generate large amounts (160-200 m3/h) of blow down water which currently is discharged in the nearby lignite power plant (UNIT IV) wastewater treatment facility. Due to the impending decommissioning of all the coal fired plants in Greece by 2030, and future stricter environmental regulations forces PPC to investigate alternative solutions. Although the blow down recycling reduces fresh water abstraction, its treatment is necessary to make it suitable for reuse in the cooling tower.
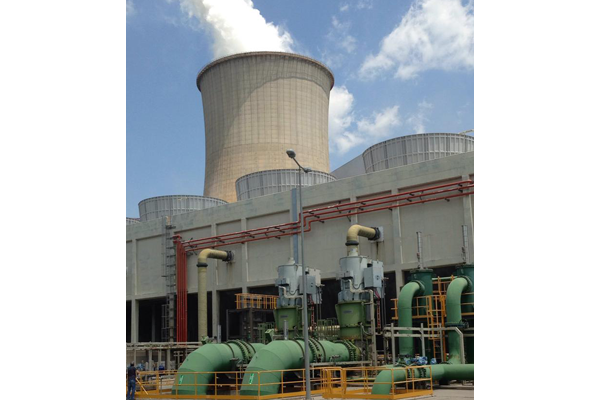
However, the CTBD water treatment presents several challenges such as high TSS, TDS, Hardness and Alkalinity, possible presence of algae and bacteria (eg. Legionella) or pathogens. Apart the above, several chemical additives maybe be introduced to impede scaling, reduce pH, inhibit corrosion, and eliminate biological contaminants (biocides). Suspended solids cause precipitation in time, which lead to scaling and fouling issues as well as erosion. Organic compounds and high temperature conditions favors microorganism growth, causing health and operation problems. All these parameters need to be controlled since affect the cooling performance.